8 Real life examples of digital innovation in construction – Constructions firms are redefining their operating models through digital innovation
Digital innovation in construction is in full flight; leading companies have recognised the benefits of implementing technologies across their operation and are realising the benefits already. The construction sector is going to change fundamentally over the next 10 years and companies who embrace new technologies are going to dominate the industry.
Cloud infrastructure makes information available anywhere across the construction site
Balfour Beatty is a great example of embracing technology and innovating operations. As a company they realised projects can be delivered more effectively and efficiently by harnessing the power of cloud computing and enhanced mobile technology. Information, data, apps and powerful analysis can be made widely available via innovative infrastructures, instantly.
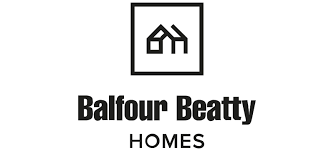
“Build right first time” with 4D Building Information Modelling (BIM), drone enabled quality control and progress tracking and fleet management through telematics
Furthermore, Balfour Beatty is using Building Information Modelling (BIM) in the form of 3D digital representations of projects overlaid with 4D detail on scheduling and cost, together with augmented and virtual reality technology which enable seamless interaction between offices and sites. Combined, this facilitates a “build right first time” approach, reducing time scales by 20% and with increases in productivity.
As the largest construction firm in the UK, they have realised using drones allows teams to track progress safely, more efficiently and with increased accuracy, collecting data more frequently than human surveyors. Drones can collect 10x more data at less than 20% of the cost of a human surveyor – a strong operational improvement and a great use case of digital innovation in construction.
Companies like Balfour Beatty and other are just starting to explore the value of telematics, which is tracking how vehicles are used, ensuring that they are driven economically, safe and sustainably. A client using telematics to capture data about its vehicle fleet can predict when maintenance is likely to be required. This has helped the client reduce instances of breakdowns by 60%.
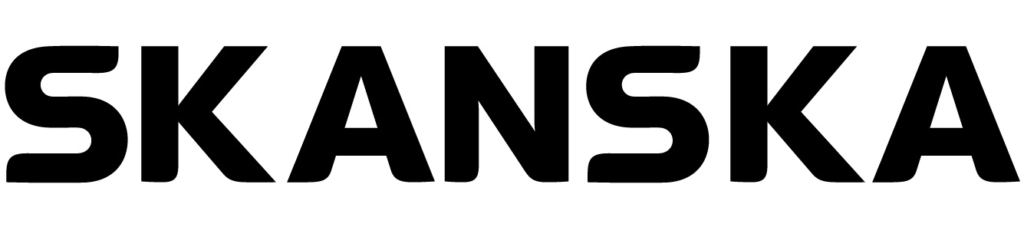
Construction firm Skanska is implementing a real-time ‘tag and track’ system of building components from the factory floor to the finished building as part of their efforts to accelerate digital innovation in construction. This system will allow real-time tracking from the supply chain to the construction phase and then onto the operations and maintenance stage providing deep insights into bottlenecks, inefficiencies and cost drives across the entire construction lifecycle.
The application of machine learning in construction is still in its early stages, but the opportunities are significant and firms have already had successful breakthroughs
Another great example of digital innovation in this space is that of a construction focused legal firm that has used machine learning technology to research version history of documents (such as contracts, meeting minutes and agendas). The company was required to process 39 million records and establish the evolution of long-term construction contracts. Faced with this challenge, they implemented a near-duplicate detection algorithm which scanned every document and clustered near-duplicate documents together based on similarity. What would have taken a team of 10 solicitors months of work, was reduced to a 3 day job for a single member of the legal team who could quickly drill down into similar documents to explore their history.
Other clients have used predictive analytics to more accurately predict the cost of new buildings and renovations up to 36 months before the project breaks ground. The ability to have predictive models which account for real market conditions (amount of construction versus labour availability) and commodity price impacts on material prices has helped firms manage their budgets from design through to construction much more efficiently.
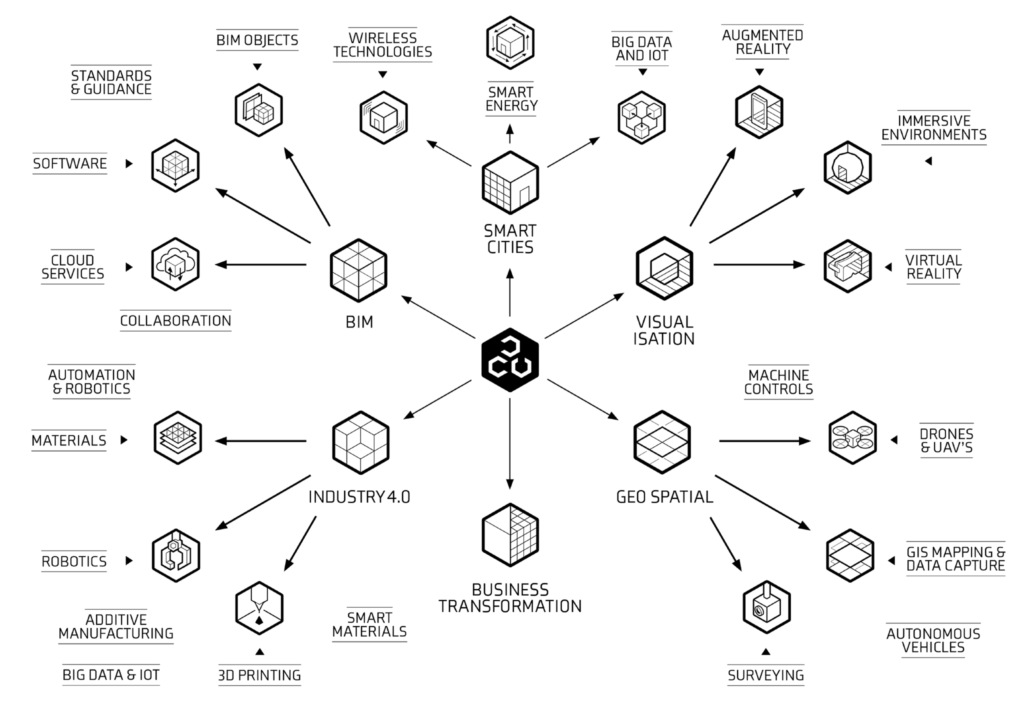
Advanced analytics and visualisation can also be used as a tool to manage and control large projects and detect issues and patterns early on. A UK construction firm, experienced water handling systems to overload because of flooding, generating unusually high maintenance requirements. Visualising these sites geographically and comparing them with historical trends enabled the impact of the abnormal weather conditions to be identified immediately. This data was then used to build a model to predict the impact of future abnormal weather pattern using radar data to trigger location specific alerts. This approach was able to reduce project delays due to abnormal weather conditions by 32% and significantly increase project controls.
In the following posts, I will analyse the business case for the implementation of these technologies individually and the type of benefits these drive to our clients bottom line.